Automatic Opening Vent (AOV) and smoke control systems are critical life safety installations in commercial, residential and public buildings. These systems are designed to remove smoke and heat during a fire, protecting escape routes, assisting firefighting efforts and limiting property damage.
A crucial component of many AOV and smoke control systems is the battery backup — the secondary power supply that ensures the system can operate even if mains power fails during a fire.
Despite their importance, batteries are often overlooked in both maintenance and compliance planning. Below, we explain why battery management is so critical, the legislation and standards that apply, and what building owners and managers need to consider.
Why Are Batteries Used in AOV and Smoke Control Systems?
In a fire, smoke can quickly block escape routes and make conditions fatal for occupants and firefighters. Smoke control systems rely on electrical motors and controls to open vents, drive fans or operate dampers.
If the primary (mains) power fails, the system must still operate. Batteries provide this vital secondary power supply, ensuring:
- Opening of vents and windows
- Operation of extraction fans
- Control signals between devices
- System feedback and alarms
Without reliable batteries, an AOV system may fail just when it is needed most.
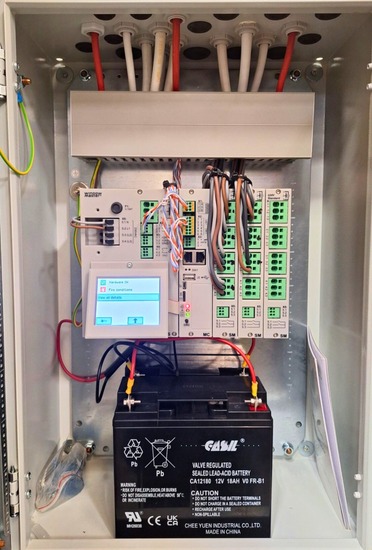
What Standards Govern Batteries in Smoke Control Systems?
Several British and European standards impose clear requirements around battery selection, installation and maintenance:
BS EN 12101-10:2014 – Power supplies for smoke and heat control systems
- Requires batteries to be appropriately marked with manufacturing details for traceability.
- States batteries must deliver the required load after considering ageing and environmental conditions.
- Demands compatibility between batteries and the overall control system.
BS 7346-8:2013 – Smoke control systems. Code of practice for planning, design, installation, commissioning and maintenance
- Requires routine inspection and testing to verify that voltages, pressures and loadings are correct.
- Stipulates that system components—including batteries—must reliably achieve the design performance within prescribed timescales.
BS 9999:2017 – Fire safety in the design, management and use of buildings
- Places responsibility on building owners to maintain fire safety systems to ensure continued reliability and effectiveness.
Regulatory Reform (Fire Safety) Order 2005 (RRO)
- Requires that fire safety measures be maintained in an “efficient state, in efficient working order and in good repair.”
- Underpins the legal duty for “Responsible Persons” to ensure that systems will work when needed.
These standards mean that traceability, performance and regular testing of batteries are legal and regulatory obligations, not optional good practice.
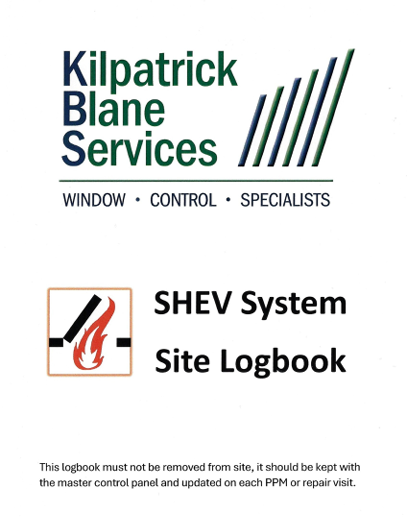
What Documentation Is Needed for Compliance?
One of the most frequent compliance failures we encounter is missing or incomplete documentation about batteries. Good practice requires:
- Date of manufacture and installation clearly marked on each battery.
- Maintenance records showing inspection and test results.
- Records of any replacements, repairs or capacity testing.
- Evidence of compliance with manufacturers’ instructions.
This documentation is critical not only for regulatory compliance, but also for insurance purposes. In the event of a fire, an insurer or investigating authority may request proof that life safety systems were properly maintained.
How Often Should Batteries Be Tested or Replaced?
Battery maintenance for smoke control systems typically includes:
- Visual inspection during routine maintenance visits for signs of corrosion, leakage or physical damage.
- Voltage checks to confirm batteries are correctly charged and healthy.
- Functional tests where the system is operated under battery power to verify that fans, vents or dampers respond correctly.
- Capacity testing (load testing) to confirm batteries can deliver required current for the specified duration.
Manufacturers’ guidance varies, but typical recommendations are:
- Replace SLA batteries every 3–5 years under normal conditions.
- Limit storage periods before installation to a maximum of 6–12 months.
- Record the installation date for warranty and lifespan tracking.
Factors that can shorten battery life include high ambient temperatures, excessive discharge events, poor charging regimes, or simply poor storage conditions before installation
What If Batteries Have No Date?
Batteries without visible manufacturing or installation dates represent a compliance risk because:
- Their age and condition cannot be verified.
- Warranty claims may be invalid if the battery fails prematurely.
- There is no way to confirm whether they have exceeded recommended storage or operational lifespan.
In these cases, the safest and most compliant action is usually to replace the batteries to ensure the system is fully operational and legally compliant.
Environmental Considerations
At Kilpatrick Blane Services, we are committed to sustainability and recognise that batteries are an environmental concern due to both production impacts and disposal requirements.
However, life safety systems cannot be compromised. Where replacement is unavoidable, we:
- Use reputable battery manufacturers with strong environmental credentials.
- Apply minimal mark-up and fair fitting costs.
- Support recycling schemes to minimise environmental impact.
Our goal is always to balance environmental responsibility with the legal and moral duty to keep people safe.
In Summary
- Batteries are critical components in smoke control and AOV systems, required to ensure operation during mains failure.
- UK fire safety law and multiple British Standards impose strict requirements for traceability, testing and documentation.
- Undated or untested batteries pose a significant compliance risk and could jeopardise safety in an emergency.
- Responsible management, testing and timely replacement of batteries is not only good practice—it’s a legal obligation.
If you have any concerns about the compliance status of your smoke control system batteries, or would like assistance with inspection, testing or documentation, please don’t hesitate to contact us. We’re here to help you stay compliant—and safe.
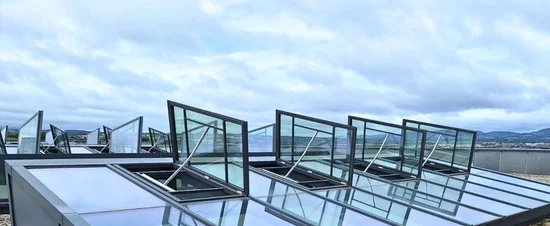